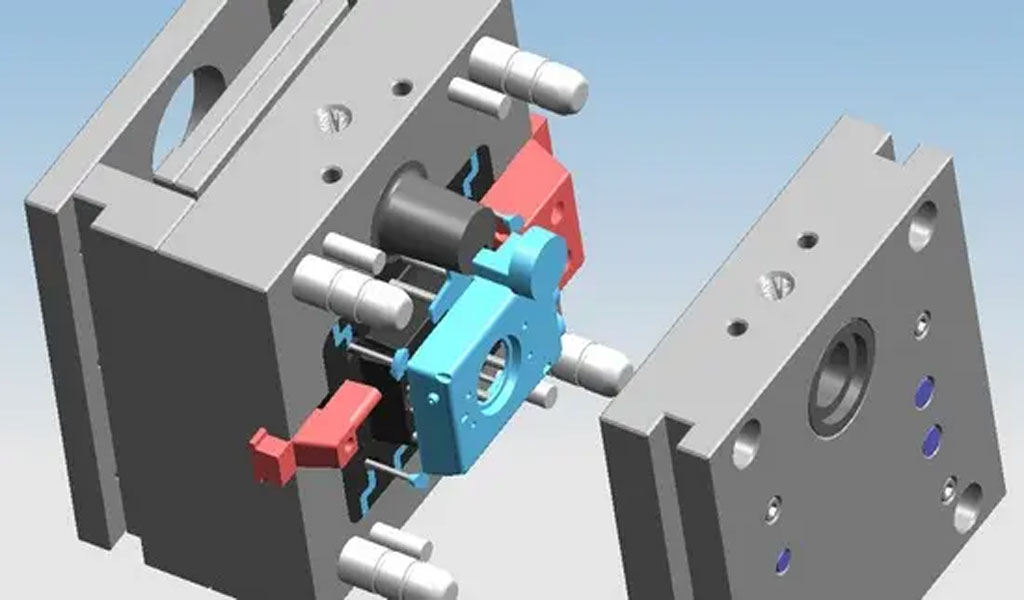
일반적인 주조 공정에서 초기 결정은 덴드라이트 방식으로 성장하고 고상 비율이 약 20%에 도달하면 덴드라이트는 연속적인 네트워크 골격을 형성하고 거시적 이동성을 잃습니다. 금속이 응고되는 동안 강한 자극이 가해지면 일반 주조시 쉽게 형성된 수지상 그물망 골격이 잔존 액상에 현탁된 분산된 입자로 부서지며, 교반하여 제조된 이 합금을 일반적으로 비수지상 반고체 합금이라고 한다. . 이 반고체 합금은 고체상 비율이 50%-60%에 도달할 때 여전히 우수한 유동성을 가지며 압력 주조, 압출 주조, 연속 주조, 진공 주조 등과 같은 기존의 성형 공정을 사용하여 금속 성형을 달성할 수 있습니다.
반고체 합금의 준비
반고체 다이캐스팅을 구현하기 위해서는 먼저 무수지상 조직을 갖는 반고체 합금 슬러리를 준비해야 한다. 반고체 합금 슬러리의 현재 제조 방법은 주로 기계적 교반 방법, 전자기 교반 방법, 변형 유도 용융 활성화 방법, 제트 주조 방법, 반고체 등온 열처리 방법, 액상 라인 주조 방법 및 화학적 결정립 미세화를 포함합니다. 방법 등
반고체 다이캐스팅 적용
반고체 다이캐스팅의 주요 시장은 꽤 오랜 기간 동안 자동차 산업이 될 것으로 예상되며 알루미늄 합금과 마그네슘 합금은 자동차 제조 산업에서 반고체 다이캐스팅의 주요 재료입니다.
다이캐스팅 프로세스 실시간 제어 연구를 통해 전체 다이캐스팅 프로세스가 동적 모니터링을 받고 다이캐스팅의 성능을 개선하고 다이캐스팅 스크랩을 줄이며 일반 다이캐스팅 기계를 만들 수 있습니다. -고체 금속 다이캐스팅 성형.
자동차 휠 허브는 대부분 강철로 만들어져 자동차의 품질을 낮추기 위해 현재 알루미늄 합금을 점점 더 많이 사용하고 있으며 성형 공정은 주로 저압 주조이지만 저압 주조는 스크랩 비율이 높고 생산성이 낮은 단점이 있습니다. 반고체 다이캐스팅 성형을 사용하면 위의 단점을 고객에게 서비스할 수 있으며 제품의 강도를 높이고 품질을 낮출 수 있습니다.
반고체 금속 성형 공정은 전통적인 가공 및 성형 기술이 가지고 있지 않은 다양한 특성과 장점을 가지고 있으며, 지난 10년 동안 반고체 성형 기술의 급속한 발전은 점차 새로운 경쟁 분야가 되었습니다. 신흥 금속 성형 기술의 세대.