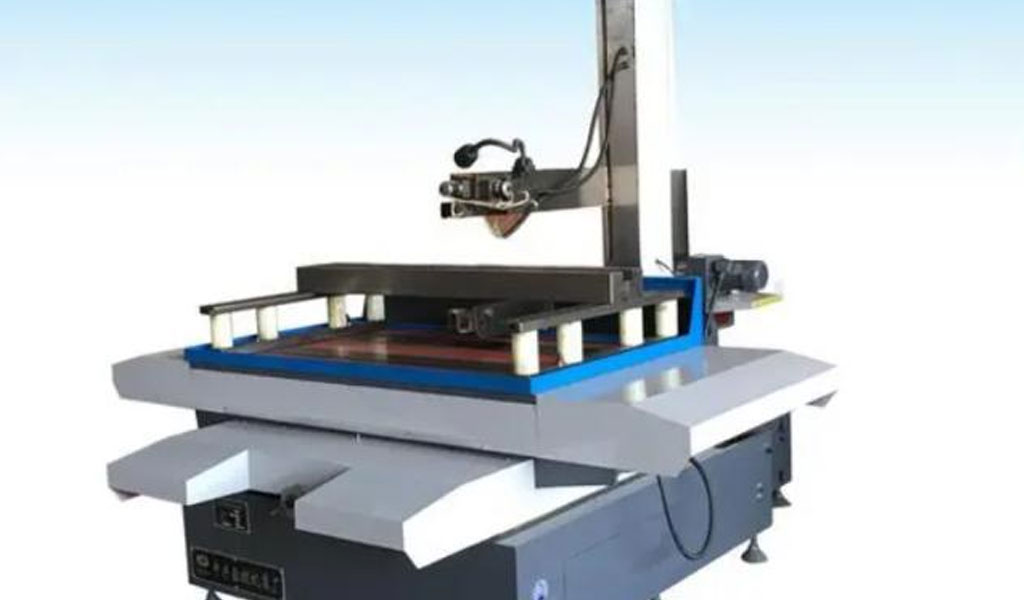
와이어 EDM은 뜨거운 칼이 버터를 자르는 방식과 유사하게 정밀하고 연속적인 와이어로 금속을 침식합니다. 와이어는 작업물과 접촉하지 않고 대신 미리 정해진 경로를 따라 재료를 증발시키는 작고 제어된 스파크를 생성하여 복잡한 모양과 날카로운 모서리를 만듭니다. 다이 싱킹 EDM도 비슷하게 작동합니다. 일반적으로 흑연이나 구리로 만든 전기적으로 충전된 전극을 사용하여 스탬프처럼 작업물에 꽂습니다. 와이어 EDM과 다이 싱킹 EDM의 차이점은 무엇입니까?
와이어 EDM과 다이싱킹 EDM의 주요 차이점
와이어 EDM과 다이 싱킹 EDM은 모두 효과적인 금속 가공 도구이지만, 원하는 결과를 얻기 위해 서로 다른 접근 방식을 취합니다. 다음은 주요 차이점에 대한 개요입니다.
차이점 1: 도구와 프로세스
와이어 EDM은 뜨거운 칼이 버터를 자르듯이 금속을 자르는 얇고 전기적으로 충전된 와이어로 간주될 수 있습니다. 일반적으로 황동으로 만들어진 와이어는 작업물에 닿지 않고 대신 미리 정해진 경로를 따라 재료를 침식하여 복잡한 모양과 날카로운 모서리를 만드는 작은 불꽃을 생성합니다. 다이 싱킹 EDM은 일반적으로 흑연이나 구리로 만든 성형 전극을 사용하여 스탬프처럼 작업물에 꽂습니다. 와이어 EDM과 같은 전기 방전은 금속을 증발시켜 점차적으로 전극 모양과 일치하는 공동을 형성합니다. 다이 싱킹 EDM은 깊은 공동과 몰드를 만드는 데 특히 효과적입니다.
차이점 2: 기능 및 응용 프로그램
와이어 EDM은 좁은 공차, 날카로운 모서리, 얇은 벽을 가진 복잡한 모양을 가공하는 데 탁월합니다. 수술 도구, 시계 부품, 복잡한 금형 인서트 제작과 같은 작업에 이상적입니다. 다이 싱킹 EDM은 깊은 캐비티, 블라인드 포켓, 복잡한 내부 기능을 만드는 데 이상적입니다. 금형 제작, 항공우주 구성 요소 및 다이 단조 응용 분야에서 널리 사용됩니다.
차이점 3: 표면 마감 및 재료 호환성
와이어 EDM의 얇은 와이어는 종종 매끄러운 표면 마감을 생성하므로 높은 정밀도와 미학이 필요한 응용 분야에 이상적입니다. 경화강, 티타늄 합금, 심지어 일부 초합금을 포함한 다양한 금속과 함께 작동할 수 있습니다. 다이 싱킹 EDM은 와이어 EDM에 비해 거친 질감을 생성하지만 여전히 좋은 표면 마감을 달성할 수 있습니다. 구리, 알루미늄 및 황동과 같은 전도성 금속과 잘 작동하지만 특정 응용 분야의 경우 추가 연마가 필요할 수 있습니다.
어떤 공정이 기계 가공 부품의 표면 마감을 더 좋게 만들까요?
와이어 EDM과 다이싱킹 EDM은 서로 다른 분야에서 뛰어난 두 가지 공정으로, 가공된 부품에 뚜렷한 흔적을 남깁니다. 그렇다면 어느 공정이 가공된 부품에 더 나은 표면 마감을 제공할까요? 세부 사항을 살펴보겠습니다.
와이어 방전 가공
경쟁사와 달리 와이어 EDM은 물리적으로 작업물에 닿지 않습니다. 얇은 전기적으로 충전된 와이어가 표면을 가로질러 움직이며 제어된 스파크로 금속을 증발시킵니다. 이를 통해 직접 접촉으로 인해 발생하는 긁힘, 홈 및 기타 결함의 가능성을 없애 더 매끄럽고 깨끗한 마감이 가능합니다. 와이어 EDM의 정밀성은 날카로운 모서리와 복잡한 세부 사항에서 빛을 발합니다. 좁은 와이어는 최소한의 홈을 남겨 섬세한 특징을 보존하는 동시에 매끄러움을 유지합니다. 따라서 표면 교란을 최소화하면서 높은 미학성을 요구하는 응용 분야에 이상적입니다.
다이싱킹 EDM
다이 싱킹 EDM은 깊은 캐비티와 복잡한 내부 형상을 만드는 데 특히 효과적입니다. 그러나 성공에는 비용이 따릅니다. 더 크고 더 단단한 전극이 작업물과 접촉하여 눈에 띄는 가공 자국과 더 거친 전반적인 질감을 남기며, 특히 모서리와 복잡한 영역에서 그렇습니다. 다이 싱킹 EDM은 구리, 알루미늄, 황동과 같은 전도성 금속에 효과적입니다. 티타늄이나 스테인리스 스틸과 같은 더 단단한 재료는 가공하기 어려워 표면 거칠기가 증가하고 재주조 층이 형성될 수 있습니다. 다이 싱킹 EDM으로 매끄러운 마감을 얻으려면 후처리가 자주 필요합니다. 높은 미적 감각이나 엄격한 공차가 필요한 응용 분야에서는 연마가 필요하며, 이는 공정에 시간과 비용을 추가합니다.
복잡한 모양이나 날카로운 모서리에는 어떤 공정이 더 적합할까요?
와이어 EDM은 다이 싱킹 EDM에 비해 복잡한 모양과 날카로운 모서리를 가공하는 데 더 적합합니다. 그 이유는 다음과 같습니다.
와이어 방전 가공
얇은 전기적으로 충전된 와이어는 비할 데 없는 제어를 제공하여 엄격한 공차와 날카로운 각도를 가능하게 합니다. 미리 정해진 경로를 따라 복잡한 형상을 쉽게 탐색하여 작은 기어, 미니어처 블레이드, 섬세한 채널과 같은 복잡한 특징을 만들 수 있습니다. 와이어의 무한한 유연성 덕분에 더 큰 전극으로는 도달할 수 없는 내부 특징과 좁은 공간에 도달할 수 있습니다. 작은 커프(절단 폭)로 복잡한 윤곽과 날카로운 각도를 절단할 수 있어 재료 낭비를 줄이고 미세한 세부 사항을 보존합니다. 와이어 EDM은 프로세스의 비접촉 특성으로 인해 버와 재주조 층이 적은 더 매끄러운 표면 마감을 생성합니다. 이는 광범위한 연마의 필요성을 없애므로 높은 미학 또는 엄격한 공차가 필요한 응용 분야에 이상적입니다.
다이싱킹 EDM
전극은 모양에도 불구하고 모서리에 사소한 불일치를 일으킬 수 있으며 좁은 곡선을 처리하는 데 어려움을 겪습니다. 복잡한 기능을 수행할 수 있지만 더 큰 크기와 접촉 제한으로 인해 극도의 정밀성에는 적합하지 않습니다. 전극의 크기로 인해 작은 공간에 대한 접근과 날카로운 내부 기능을 만드는 능력이 제한됩니다. 깊은 구멍과 복잡한 모양을 처리할 수 있지만 복잡한 구석구석에 도달하는 것은 어려울 수 있으며 여러 개의 전극이나 추가 마무리 공정이 필요할 수 있습니다. 다이 싱크 EDM: 전극 접촉으로 인해 특히 모서리와 복잡한 영역에서 눈에 띄는 가공 표시가 있는 거친 질감이 발생할 수 있습니다. 연마는 마무리를 개선할 수 있지만 시간과 비용이 더 많이 필요합니다.
결론
각 방법에는 장단점이 있습니다. 차이점을 이해하면 특정 프로젝트 요구 사항에 가장 효율적이고 비용 효율적인 EDM 프로세스를 선택할 수 있습니다. PTJ은 고급 와이어 EDM 기계로 와이어 EDM 서비스를 제공합니다. EDM 전문가 와 프로젝트 요구 사항을 논의할 때 다양한 방법을 철저히 이해하면 정확한 의사 소통이 보장되고 오해를 피할 수 있습니다. 이를 통해 보다 효율적인 협업과 더 나은 결과를 얻을 수 있습니다.